
In the race to Net Zero, perhaps it's time to look at how plastic could become a carbon sink storing CO2 produced by other more polluting materials such as steel and cement.
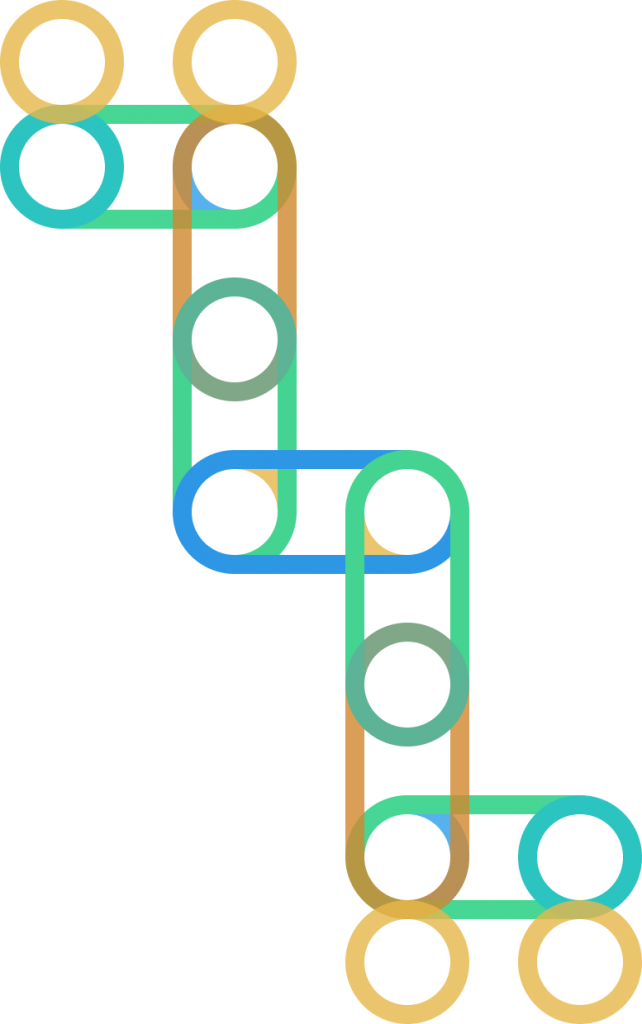
As plastic has replaced materials like glass, wood, steel and aluminum in almost every area of our lives its production and usage continues to accelerate.
Over the past four decades, global plastics production has quadrupled creating a trend that if it were to continue, would plot the plastic industry’s GHG emissions on a path to reach 15% of the global carbon budget by 2050.
Studies put the plastic industry’s total GHG emissions at 1.9 Gt of CO2-equivalent (CO2e) in 2015, accounting for almost 4.5% of total GHG emissions of 47Gt of CO2-equivalent (CO2e), with its carbon footprint forecast course to grow to 6.5 GtCO02e by 2050.
This accelerated trend coupled with the environmental impact of plastic waste has heralded campaigns for a move away from plastic use and replacement by other materials even when doing so would most likely have a negative impact on the fight against climate change with plastic alternatives like glass, aluminum and paper, generating up to four times the environmental impact in terms of GHG emissions, according to studies by Trucost.
Furthermore, ironically, it is the material’s ability to reduce the carbon footprint of other industries – the automobile industry and the food industry, for example – that is largely behind its global growth in popularity.
But what if the success of plastic could in fact be a gilded opportunity to capture and store carbon produced by even more polluting materials such as the steel and cement industries?
Carbon dioxide utilization (CO2U) technologies are already being used to prevent carbon produced by industries such as cement and steel (both responsible for approximately 7% of global GHG emissions) from entering the atmosphere.
The same technologies have been used to pull carbon out of the air and convert it into useful precursor chemicals that can be converted into products that have the potential to become a carbon trap during their useful lifetime or in their post-consumer life if they are sent to landfill.
As we are learning with extreme weather events, global climate change is largely about where to store carbon on the planet’s four principal compartments: the atmosphere, biosphere, hydrosphere and geosphere.
Currently much of the carbon being produced is being stored in the atmosphere resulting in global warming and all the consequences that come with that.
There is, however, another place that carbon can be stored: the technosphere which comprises all the technological objects manufactured by humans, many of which are increasingly manufactured with plastic components.
While plastics today are mainly made from carbon that comes from crude oil and natural gas, they can also be produced using biomass or biomaterials, which draws carbon from the atmosphere.
Through the conversion of biomass to plastics, carbon is transferred from the biosphere to the technosphere, where it can be recycled repeatedly in the case of plastics like PET or for other less easily recyclable plastics locked into building materials or stored in secure landfill.
So how does it work and what potential does plastic have to become one of the world’s most important and efficient carbon sinks?
What is Carbon Dioxide Utilization?
Carbon dioxide utilization (CO2U) technologies are a subset of carbon capture utilization and storage (CCUS) technologies and refer to the productive use of anthropogenic CO2 to make value-added products such as building materials, synthetic fuels, chemicals, and plastics.
CCUS technologies have already been deployed around the world at scale and are seen as a crucial tool to decarbonize the world’s economy.
As well as storing CO2 in the subsurface, there has been increasing interest in its utilization. CO2U can promote not only a more circular economy but also, in some cases, result in products with enhanced properties or processes with lower feedstock costs.
According to IDTechEx, the global carbon dioxide utilization market is set to exceed $485bn by 2042.
Currently, according to the International Energy Agency, the technology is being used at an industrial scale in a handful of industries with the agency estimating that CCUS facilities currently capture almost 45 Mt CO2 globally with around 35 commercial facilities applying CCUS to industrial processes, fuel transformation and power generation.
In the plastics space, successful deployment of CO2-based polymers has been growing from a similarly small base with over 250,000 tonnes of CO2 being used as a raw material in polymer manufacturing worldwide each year.
While this is still tiny compared to the 460m tonnes of plastics produced each year, there’s no shortage of optimism for the technology as one of a host of silver bullets with enormous potential for the circular, zero-waste economy.
“With a total annual capture capacity of almost 45 Mt CO2, CCUS deployment has been behind expectations in the past but momentum has grown substantially in recent years, with around 300 projects in various stages of development across the CCUS value chain,” says the IEA.
Project developers have announced ambitions for over 200 new capture facilities to be operating by 2030, capturing over 220 Mt CO2 per year. However, only around 10 commercial capture projects under development have taken a final investment decision as of June 2022.
Nevertheless, even at such a level, CCUS deployment would remain substantially below what is required in the Net Zero Scenario.
Carbon Dioxide Utilization for PET Plastic
In particular, recent advances in microbiology, metabolic engineering and electrochemistry have made the carbon negative production of simple one and two carbon compounds.
Acetogens, in particular, can convert flue gas into ethanol and acetate creating an opportunity for the chemical industry with several commercial plants in development.
A secondary development is advances in electrochemical carbon capture which can convert CO2 into small carbon compounds like formate and ethanol with increasing efficiency.
To the extent that the electrical power is derived from the sun or nuclear plants, electrochemistry provides another carbon negative process for making simple carbon compounds.
Effective ways to upgrade these simple molecules into more complex chemicals could therefore potentially form the basis for a carbon negative chemical industry.
These compounds can be used in the production of PET and pilot schemes are already under way to create bottles with CO2 outputs from other industries.
Leading the field is Illinois-based company, LanzaTech, which in partnership with Migros and Danone has produced PET bottles from CO2.
Its early-stage proof of concept work first announced in October 2021 has evolved throughout 2022 to show for the first time that it is possible for a bacterium to directly produce MEG from gas.
Its partnership with Danone to produce PET bottles converts carbon emissions from steel mills or gasified waste biomass directly into MEG.
The carbon-capture technology uses a proprietary engineered bacterium to convert carbon emissions directly into MEG through fermentation, bypassing the need for an ethanol intermediate, and simplifying the MEG supply chain. The direct production of MEG was proven at laboratory scale and the presence of MEG was confirmed by two external laboratories.
“The science is state-of-the-art, but the idea is simple. We use nature to heal nature. Carbon emissions are fed to trillions of carbon-hungry microbes that turn pollution into valuable raw material commodities,” says LanzaTech CEO Dr Jennifer Holmgren.
“Ethylene production is one of the three largest carbon emitters in the chemical industry. Now is the time to break free from relying on virgin fossil inputs as a feedstock for the things we use in our daily lives,” she says.
“With the ability to directly produce this bulk chemical commodity, we aim to make synthetic biology accessible and bring it to the people in everyday consumer goods. This is not a specialty chemical or a niche market, rather it is something that we believe will have a significant impact in the lives of billions of people daily, no matter how much you earn or where you live. This is an exceptional opportunity to implement meaningful carbon removal and create sustainable synthetic chemicals that we believe can replace fossil fuels forever.”
LanzaTech’s first two commercial scale gas fermentation plants have produced over 50 million gallons of ethanol, which is the equivalent of offsetting the release of 200,000 metric tons of CO2 into the atmosphere.
Bioplastics and Carbon Capture
The technology represents the most ambitious and least controversial element of a movement away from fossil fuel feedstocks towards the introduction of biomass in plastic production.
Alternative biological sources for bioplastics include sugar cane and other agricultural commodities that bring with them fears about competition for land and resources used to feed the world’s population.
“Exclusive dependence on biological sources of carbon feedstock is risky, but by expanding the use of captured CO2 (enabled by a clean hydrogen economy), the plastics system could strategically reposition itself as a carbon sink and enabler of climate change mitigation,” says Yoni Shiran, plastics lead at SYSTEMIQ, the author of a recent report on plastic’s path towards net zero emissions by 2050.
SYSTEMIQ’s ReShaping Plastics report has plotted a clear path for how the industry can work to get to net zero by 2050.
Carbon capture technology, whilst beautifully circular in theory, however, faces plenty of challenges.
Making chemicals that capture emissions faces two principal hurdles, according to industry experts, namely reducing costs sufficiently to compete with petroleum-based chemical manufacturing and sourcing enough captured emissions or raw materials.
“The market for captured-carbon-based fuels and products is still relatively limited due to technology and cost constraints,” says Mitch Toomey, vice president of sustainability and responsible care at the American Chemistry Council trade association.
Analysis by Paul Stegmann, Vassilis Daioglou, Marc Londo, Detlef P. van Vuuren and Martin Junginger showed that a circular bioeconomy approach combining recycling with higher biomass use could ultimately turn the sector into a net carbon sink, while at the same time phasing out landfilling and reducing resource consumption.
“Using biomass as feedstock and circular economy (CE) measures such as recycling are two options that may substantially reduce both fossil feedstock use and the related GHG emissions of the plastics sector,” they write in a recent article published in Nature.
“Together, these could contribute to a circular bioeconomy (CBE) for plastics, potentially even achieving negative CO2 emissions by sequestering biogenic carbon in plastic products for long-term use.”
They estimate that if non-biodegradable, bio-based plastics were to replace fossil fuels as feedstock for plastic production, it could effectively sequester the equivalent of 275 Gt of negative CO2 emissions, almost nine times current global annual energy-related emissions in the next 80 years.
For this to happen, however, they argue, special conditions need to be created. Firstly there needs to be greater regulation of fossil fuel prices via a uniform carbon price that would facilitate GHG emission mitigation and incentivize the decarbonization of the energy industry.
But a carbon price alone would not be enough, “further policy measures are necessary to speed up biomass deployment in the plastic sector, such as subsidies for biomass use.
In addition, carbon capture (and utilization) during plastic production should be considered, to further reduce the sector’s GHG impact,” writes Stegman et al.
For plastic to become a carbon sink a paradigm shift in recycling would be required for plastics currently not recycled as much as PET. Doing this will require mechanical recycling and chemical recycling to push industry recycling levels up to 70%, levels achieved by PET but rarely achieved in other plastic categories.
As Yoni Shiran says: “What is lacking is policy frameworks, it’s economic incentives, it’s the right business models, it’s the right finance mechanisms. So these are the things that are missing in the system. These are things we can turn to. Yes, we can always improve on technology and we should definitely invest in R&D. Technology is important, but let’s not wait for technology. We have plenty of technology to get started. We need to make sure we have the right incentives in the system and the right policy frameworks.”
Companies Making Waves with Carbon Capture
LanzaTech
Carbon recycling company, LanzaTech, captures industrial carbon emissions and converts them into ethanol using a unique biological process. In a partnership with Total it converts the ethanol into ethylene before polymerizing it into polyethylene that has the same technical characteristics as its fossil counterpart. L’Oréal uses this polyethylene to produce packaging with the same quality and properties as conventional polyethylene. It is a technological and industrial success proving that industrial carbon emissions can be used to produce plastic packaging. This world first demonstrates the commitment of the three partners to the development of a sustainable circular economy for plastics and paves the way for new opportunities for the capture and re-use of industrial carbon emissions.
Founded in New Zealand in 2005, LanzaTech is a leading Carbon Capture and Transformation company combining synthetic biology and engineering to transform waste carbon into materials and high-value products representing a total addressable market opportunity of over $1 trillion, including sustainable fuels, fabrics and packaging that people use in their daily lives. LanzaTech is based in Illinois, USA and employs more than 170 people, with locations in China, India and Europe.
More info: https://lanzatech.com
Newlight
The company took about a decade to develop a process using microbes that suck up methane or carbon dioxide to grow a biological material called polyhydroxybutyrate, which is used to make biodegradable resins that can replace plastic. It now sources captured emissions from dairy farms, ethanol plants and landfills, and is expanding into coal mines and exploring direct-air capture. Newlight in 2020 opened its first commercial-scale factory in Huntington Beach. It manufactures foodware, such as cutlery, bowls and straws, for Shake Shack Inc., Walt Disney Co. and Hyatt Hotels Corp. among others. Newlight said the factory has produced more than 50 million foodware units.
Newlight’s next factory is slated to come online in 2025 in Ohio, which will tap methane from a coal mine through an agreement with CNX Resources Corp. The CNX deal will supply between 1 million to 36 million metric tons of carbon-dioxide equivalent.
More info: https://www.newlight.com/
Origin Materials
Origin Materials has a different approach acquiring captured emissions and plans for its first commercial-scale factory to come online next year. The West Sacramento-based company already has $9 billion in orders from companies including Primaloft to make bedding and apparel and Ford for automotive parts, and expects to be profitable by 2025 after its second commercial-scale plant opens. Through a chemical process, Origin Materials converts organic materials, which lock up carbon dioxide from when they were growing, for use in polyethylene terephthalate, or PET, plastic commonly found in packaging and other synthetic products. The company’s offerings will be cost competitive with petroleum-derived versions because the ingredients it uses are abundant and cheap, co-CEO John Bissell said. “There are a lot of these materials globally,” Mr. Bissell said. “If we’re at the point that we are using all of those things, we’ve won the game if we are starting to run out of feedstock.”
More info: https://www.originmaterials.com/
Avantium
The Amsterdam-based company has developed a program – dubbed Volta – that uses electrochemistry to turn CO2 into sustainable chemicals and materials.
“The technology uses renewable electricity to directly convert CO2, making it the perfect combination of renewable energy and a climate-friendly feedstock. Additionally, this technology produces high value ingredients, chemical building blocks and fuels, all without using a single drop of oil pumped from the ground,” says Avantium’s lead on the Volta project, Arnaud Mol.
“The development of electrochemistry has the potential to use CO2 as a feedstock for the sustainable production of chemicals and materials and is seen as a ’game-changer’ for the chemical industry. The result is that greenhouse gas is sequestered into products that can replace plastics and chemicals that are now produced from fossil feedstock.”
Avantium is currently constructing the world’s first commercial plant for the production of FDCA (furandicarboxylic acid) from plant-based sugars in Delfzijl, The Netherlands. FDCA is the key ingredient for making the plant-based, highly recyclable plastic material PEF, which has superior performance properties compared to today’s widely used petroleum-based packaging materials. Avantium expects to open this FDCA Flagship Plant by the end of 2023, enabling the commercial launch of PEF from 2024 onwards.
More info: https://www.avantium.com
Share it
THE HISTORY OF PLASTIC
Throughout the history of plastic, PET has been crucial in keeping food fresh with lightweight and durable packaging solutions that have helped reduce food waste for almost a century. Learn all about the invention of plastic and the important role it has played feeding people and saving the lives of humans and elephants in the adaPETation® timeline of the history of plastic.