
The adoption of biobased products and solutions by the plastic packaging industry is a key element to reduce its carbon footprint and curb the environmental impacts of plastic waste.
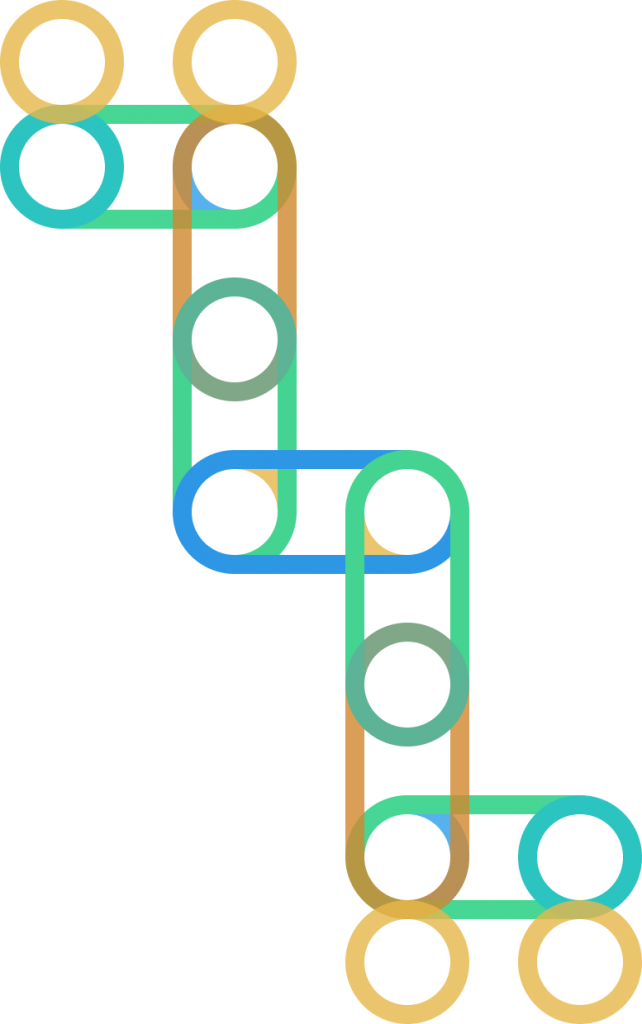
While still relatively small in its overall participation in the global production of plastic packaging, bioplastics, biodegradable packaging and other nature-based solutions, offer enormous potential for reducing the industry’s reliance on virgin fossil fuel feedstocks.
Whether it is the upstream decoupling of plastics packaging from fossil fuel feedstocks or the deployment of natural enzymes to accelerate the depolymerization of the material further downstream, nature has a big role to play in making PET even more friendly.
At the top of the food chain, global bioplastics production capacity is set to increase from around 2.1 million tonnes in 2020 to 2.8 million tonnes in 2025, impressive growth but still representing less than 1% of the world’s global production output.
Bio-based, non-biodegradable plastics, include drop-in solutions like bio-based PE and bio-based PET (polyethylene terephthalate), as well as bio-based PA (polyamides), which currently make up for 40% (0.8 million tonnes) of the global bioplastics production capacity. These bio-based products use biological feedstocks instead of fossil fuels, to create polymers with the same attributes as fossil-fuel feedstocks.
The other more innovative biopolymers, PP (polypropylene) and PHAs (polyhydroxyalkanoates) are driving the growth in the uptake of bio-based solutions.
Production facilities of PHAs are set to grow sevenfold in the next 5 years. These “biodegradable” plastics account for 60% of the global bioplastics capacities today.
While they can be composted in special conditions these solutions remain far from what some would consider “biodegradable”, due to the shortage of industrial composting facilities capable of breaking down the polymers.
Bioplastic Challenges
Often “biodegradable” plastic items (including single-use plastic bags and containers) break down completely only if exposed to prolonged high temperatures above 50°C (122°F). Such conditions are met in incineration plants, but very rarely in the environment. Therefore, even bioplastics derived from renewable sources (such as corn starch, cassava roots, or sugarcane) or from bacterial fermentation of sugar or lipids (PHA34) do not automatically degrade in the environment and especially not in the ocean.
These natural solutions also complicate recycling streams of other traditional PET if they are mixed, another reason this solution has struggled to displace in significant quantities traditional fossil-fuel polymers.
They do offer a glimpse of how the packaging industry could break its reliance on fossil fuel feedstocks. With solutions like PEF which is based on furanics technology, reportedly reduces non-renewable energy use by 40–50% and greenhouse gas emissions by 45–55% compared to fossil-fuel based PET.
Improvements in cellulose conversion technology used in the extraction of cellulose from non-food crops such as corn husks, grass and wood is expected to improve the quality and quantity of bioplastics available and reduce their manufacturing costs through yield improvements.
Some of the world’s largest consumer goods brands have explored the switch to bio-based solutions, but global brands like Coca-Cola have found it challenging to scale up their use of bio-PET to achieve ambitious goals set in 2014 to make all of its bottles 100% bio-based by 2020.
The soft drinks giant launched its “PlantBottle” in 2009, a bottle made of 30% plant-based PET and 70% purified terephthalic acid (PTA). By 2015 it was producing a fully recyclable, PlantBottle with 100% plant-based material but it has failed to hit it’s goal in having all new PET plastic bottles made from the bio-based technology by 2020. While the bottles are used widely across its brands, PlantBottle packaging still accounts for as little as 30% of the company’s packaging volume in North America and 7% globally.
The world’s largest producer of plastic packaging uses 3m tonnes of plastic a year but still struggles to generate the kind of scale required to bring costs down to comparable levels to traditional PET.
In 2018, it took the unusual step of sharing its proprietary technology with “non-competitive” companies and brands including Heinz Tomato Ketchup and Ford, in the hope that it will encourage wider use of bioPET by companies both inside and outside the beverage industry, helping to scale up demand and, in turn, drive down pricing for bioPET.
Depolymerization & Infinite PET Circularity
Some of its biggest rivals have also embraced biological solutions further downstream, teaming up with French company, Carbios, to put nature back into the equation to deal with post-consumer plastic.
Working with a consortium that includes L’Oreal, PepsiCo, Suntory Beverage & Food Europe and Nestlé Waters, Carbios has developed a new depolymerization process that “supercharges” an enzyme that occurs naturally in compost heaps to break down leaf membranes of dead plants.
The process breaks down 97% of plastic in just 16 hours, which the company estimates is 10,000 times more efficient than any biological plastic recycling trial to date. Offering the possibility of making PET plastic infinitely recyclable, is a game-changer according to Carbios’ CEO Jean Claude Lumaret.
“In a world first, we have created food-grade clear bottles from enzymatically recycled colored and complex plastic with identical properties to virgin PET, and in partnership with the Consortium, we have proved the viability of the technology with the world’s leading brands. This is a truly transformational innovation that could finally fully close the loop on PET plastic supply globally, so that it never becomes waste,” he says.
Carbios has been working on this solution for 10 years and there are a plethora of other examples of how nature can take the lead on the problem in the pipeline. Scientists are exploring the use of bacteria found in cow stomachs that can be used to digest polyesters used in textiles, packaging, and compostable bags, according to a new study by the open access publisher Frontiers.
Microbial communities living inside the digestive system of animals have shown promising signs of being able to do much of the heavy lifting when it comes to breaking plastic down into its original components.
Researchers in the US and the UK are also experimenting with a bacterial microbe, PETase, that was discovered to eat PET plastic in a recycling plant in Japan in 2016.
These depolymerization solutions offer PET producers and brands to break free of the current limitations of mechanical recycling.
“The problem with mechanical recycling is that it involves crushing the material and shredding it, melting it down and converting it into a new product, but the new products are of a lower quality they don’t have the same mechanical properties or thermal properties that the original material did so you are downgrading the material over time,” says Erica Ericksson lead researcher at the National Renewable Energy Laboratory looking at the use of PETase in biological recycling processes.
“Statistically when you look at the larger system materials might get recycled once maybe less than that and only about 20% of the materials that are made in this polymer class either actually enter a recycling stream so we have a large resource that we can tap into and approach this in a different way, potentially that would result in even more recovery of the original material meaning that you have to dip into other resources even less,” she says.
In September 2021, Carbios will start construction of its first industrial plant, before launching a 40,000 tons capacity industrial facility, by 2025. All of the natural solutions working their way down the PET pipeline will need to scale rapidly to enable fast moving consumer brands to hit pledges made under Plastic Pacts, to make all of their plastic packaging recyclable or reusable by 2025.
“It is really exciting to be a part of this and there’s a lot of people in the global community in science and industry working on the same thing and it’s starting to see movement and a collective effort towards this goal,” says Ericksson, “I do draw a lot of reassurance that we can come together as people of the globe to address this problem from a lot of different aspects so the work that I am doing is one of many different approaches or strategies.”
Share it
Useful Links
THE HISTORY OF PLASTIC
Throughout the history of plastic, PET has been crucial in keeping food fresh with lightweight and durable packaging solutions that have helped reduce food waste for almost a century. Learn all about the invention of plastic and the important role it has played feeding people and saving the lives of humans and elephants in the adaPETation® timeline of the history of plastic.