
From take-make-dispose to a re-cyclical model, PET holds the key to reaching the world’s recycling goals.
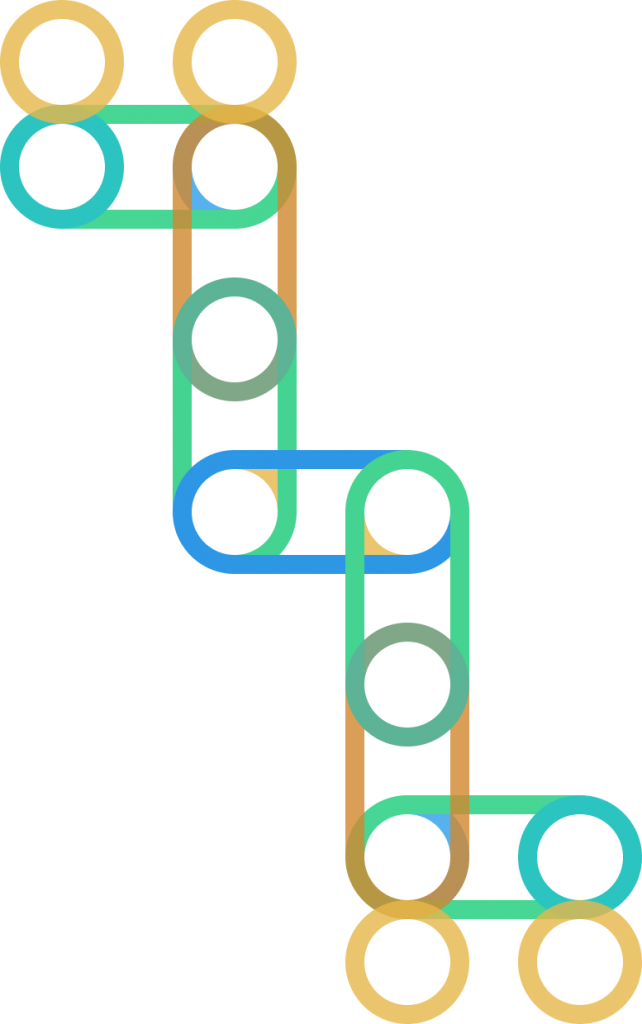
The world has had a logo for recycling since 1970, when student Gary Anderson won a competition to design a symbol with his easily recognisable Mobius loop. Sponsored by the Container Corporation of America, it was hoped that the competition would kickstart a journey to close the loop on plastic production.
Anderson’s logo makes it all look so easy. Easy as 1-2-3. Sort, collect, recycle and yet half a century later, we’re still failing to collect and re-use more than 82% of the world’s plastic waste. Some countries like the United States still send 70% of the plastic collected for recycling to landfill.
While in Europe, recycling sits at around 42% and the amount of plastic collected for recycling is going to landfill is lower (30%), the world’s largest waste producers are still a long way from closing the loop on plastic production and putting plastic waste back into the supply chain in any significant way.
It was China that finally shone a light on the world’s failings when it comes to recycling. It’s decision in 2017 to stop importing plastic waste (implemented in 2018), blew the lid off a fundamentally flawed recycling system where the world’s largest producers of plastic waste sorted their trash only to export it to countries with waste management systems that were unable to cope with the volume of waste.
Exporting the problem resulted in as much as 13 million tonnes a year of plastic waste finding its way into our oceans. Further attention has been brought to the failings of the industry with information recently published by the Minderoo Foundation that shows that the 100 largest polymer producers all continue to rely almost exclusively on “virgin” (fossil-fuel-based) feedstocks. In 2019, production of recycled polymers from plastic waste – a “circular” model – accounted for no more than two per cent of total output.
“There is a consensus that plastics are an unsustainable material. And yes, plastics are certainly an enormous problem, but they don’t necessarily have to be. The main issue is with our linear economic model: goods are produced, consumed, then disposed of. This model assumes endless economic growth and doesn’t consider the planet’s exhaustible resources,” says Sibele Cestari, Research Fellow in Polymeric Materials at Queen’s University Belfast.
At times deciding who is to blame for this collective failure has felt more important in the conversation than finding solutions that will have a lasting impact.
Consumer goods companies push responsibility onto their customers whilst environmental activists put the blame squarely back onto brands and polymer producers, lobbying for extended producer responsibility laws to push the task of cleaning up plastic waste onto those that profit from its sale.
Inspirational Upcycling
The tiresome blame game has left forward-thinking companies and activists to take matters into their own hands, deploying biomimicry principles and copying nature’s ability to turn abundance into more abundance.
These organizations see in one man’s trash another man’s treasure and are setting an important marker for others to follow. Organizations like Precious Plastic, have mobilized an army of activists, unleashing a grass-roots movement to find collaborative ways to eat their way through every type of plastic that has already lived its first “useful life” and is now in need of up-cycling or recycling into something else.
Other pioneers like carpet manufacturers Interface and Mohawk have focused on up-cycling polyethylene terephthalate (PET) bottles into carpets, the latter up-cycling 28 billion bottles since it was founded in 1999. They’ve been joined by eco-friendly fashion brands, Bionic Yarn and Rothy’s who have, in turn, inspired an army of others to follow suit and give PET plastic bottles a longer, second life cycle.
Increasingly consumers have responded favorably by switching their allegiance to brands that are doing something to address the problems we face as a species.
Given the mountains of plastic to be recycled and the giant opportunity that this presents, investment continues to gather pace, although challenges remain with some plastics being harder to recycle than others.
Globally recognized as the cleanest of the plastics, PET is a safe, non-toxic, strong, flexible material which is 100% recyclable making it the material of choice for the burgeoning recycling industry.
Recycling of PET compares favorably to that of other materials like aluminum and paper with 58% of all PET bottles currently recycled in Europe. The figure is as high as 85% in Japan, a number that the European Union has set itself the goal of surpassing by 2029.
Over 67% of all local authorities in the US now offer collection facilities for these plastics, the lion’s share are plastic bottles and food packaging.
While collection of this abundant material is becoming more efficient and the plethora of inspirational initiatives converting plastic waste into popular products, these innovative brands are swimming against the tide of an unrelenting flow of single use plastics.
Plastic production doubles almost every 10 years. The number of plastic bottles produced globally this year is expected to reach 583.3 billion. More than half of the plastics ever produced have been shipped in the last fifteen years.
If recent trends continue 28 billion tonnes of plastic will be produced in the next 30 years. So even if toy maker, Lego does eventually work out how to convert PET bottles into its distinctive bricks, all of these well-meaning upcycling initiatives are unlikely to leave a dent in the flow of fossil-fuel based polymers being pushed into the system.
If the industry is to become circular, it’s going to need to break its dependence on virgin polymers produced from fossil fuels.
Bottles made of PET can be recycled into the same form – a new beverage bottle – again and again, neatly closing the recycling loop and enabling ‘cradle to cradle’ packaging solutions. Chemical and mechanical recycling measures sitting alongside each other are being explored to ensure that more PET bottles and packaging are made from recycled bottles.
Regulators Give Recycling a Boost
One of the challenges is that it continues to be far cheaper to produce single-use plastics from fossil fuels than from “green” feedstocks than to produce them from recycled plastic waste.
The cost of door-to-door collecting, sorting and recycling of household plastic waste versus the economies of scale enjoyed by virgin polymer producers with ready access to fossil fuels via purpose-built pipelines. As a result, the single-use plastics thrown away have little to no value because there is limited demand for them. And without a commercial incentive to collect waste, collection rates are largely dependent on the availability of public funding.
Tired of picking up the bill for this cleanup operation, governments in Europe have provided an incentive for producers to invest in recycling by introducing the EU Single-Use Plastic Directive in 2019 which requires all PET bottles to contain 25% recycled polymer by 2025 and all plastic bottles to contain 30% recycled content by 2030.
The directive it is estimated will raise €8 billion a year to be used in the EU’s rebuilding program post-COVID 19 with a tax of €800 / tonne levied on plastic production that does not comply with this mandatory recycled content. In the UK, the government will charge producers of plastic that do not contain 30% recycled plastic a tax of £200 / tonne.
The regulation has sparked an acceleration of closed-loop recycling investments by the world’s largest producers in Europe.
Plastics Europe estimates that producers will increase their investments in chemical recycling and depolymerization plants in Europe from €2.6 billion in 2025 to €7.2 billion in 2030 with chemical recycling producing 1.2 million tonnes (m/t) of recycled plastic in 2025 and 3.4 m/t in 2030.
By 2050, nearly 60% of global plastics production could be based on reuse and recycling, according to Plastics Europe president Dr Markus Steilemann. “Chemical recycling is a game changer and a key building block of the circular economy – not only in Europe. This increased investment confirms the determination of the industry to address the problem of plastics waste and supports the EU Green Deal’s climate and sustainability ambitions.”
America’s plastic makers have set a goal for all plastic packaging used in the US to be reused, recycled or recovered by 2040. Since China stopped importing the country’s plastic waste, 66 projects worth more than $5.5 billion in chemical and mechanical recycling investments have been announced in the US.
Some Loops are Bigger Than Others
With an intense focus on both chemical and mechanical recycling, as a crucial part of closing the loop on plastic production, there’s another form of recycling that is being heralded as an even more efficient step towards less waste.
Product designers at the largest consumer goods brands are seeking to shorten the loop even further by introducing reuse systems that could reduce the need for recycling on such an industrial scale for certain plastic products.
Reuse systems like the good old bottle deposit systems used in the past, have already gained traction in developed countries where companies like Terracycle’s Loop and Algramo are rolling out new technology to reduce significantly single-use plastics.
Timur Zilbershteyn, Principal Analyst, Chemicals and Polymers at Wood Mackenzie says the expansion of reuse systems could reduce demand for polymers and the demands placed on the recycling sector by 12% by 2040.
“By removing the necessity for this reprocessing, reuse models – where applicable – are the more sustainable, circular solution,” he says. “A packaging value chain optimised for sustainability, would therefore look to redesign that proportion of plastic packaging that is suitable for reusable applications.”
Wood Mackenzie’s research on the subject, however, pointed to the systems being less relevant in developing countries which will limit its overall impact.
“The total demand for all polymers in packaging in the base scenario for 2020 is about 88 million tons, and by 2040 it is expected to grow to 162 million tons per year. The re-use scenario expects that the number will be lower, around 153 million tons, taking into account both the loss of single-use demand and the addition of reusable packaging demand,” says Zilbershteyn.
“For high-income countries, the number for 2020 is 29 million tons, and the base scenario assumes it will be about 36 million tons in 2040. In the reuse scenario, it will be about 31 million tons in 2040, reversing the growth to negative somewhere in the 2030s,” says Zilbershteyn.
Retailers and consumer goods companies like Unilever are backing this solution redesigning their packaging to allow it to explore reusable containers in Europe, the UK and USA. Germany has already mandated that all food retailers need to offer a reusable alternative to single-use packaging by 2022.
According to Wood Mackenzie’s research, polymers that are exposed to short-term, rigid applications would be the most affected by the adoption of reuse models.
Consequently, PET, PP and PS are most vulnerable to the growth or re-use models in high income countries and could experience an overall decline in demand of up to 25% if the reuse model is scaled successfully to replace single use plastics used for water and beverages and plastic containers and trays.
“For PET and especially PP, the decrease in shorter duration packaging demand is partially offset by the demand for reusable packaging” says Zilbershteyn, “to increase durability, this packaging will generally have thicker walls, and therefore requires more polymer per unit. However, the net impact is negative for polymer demand, even accounting for the additional polymer required for these applications.”
Share it
Useful Links
THE HISTORY OF PLASTIC
Throughout the history of plastic, PET has been crucial in keeping food fresh with lightweight and durable packaging solutions that have helped reduce food waste for almost a century. Learn all about the invention of plastic and the important role it has played feeding people and saving the lives of humans and elephants in the adaPETation® timeline of the history of plastic.