
Full circularity appears to be on the horizon but what can we expect from the more advanced recycling technologies?
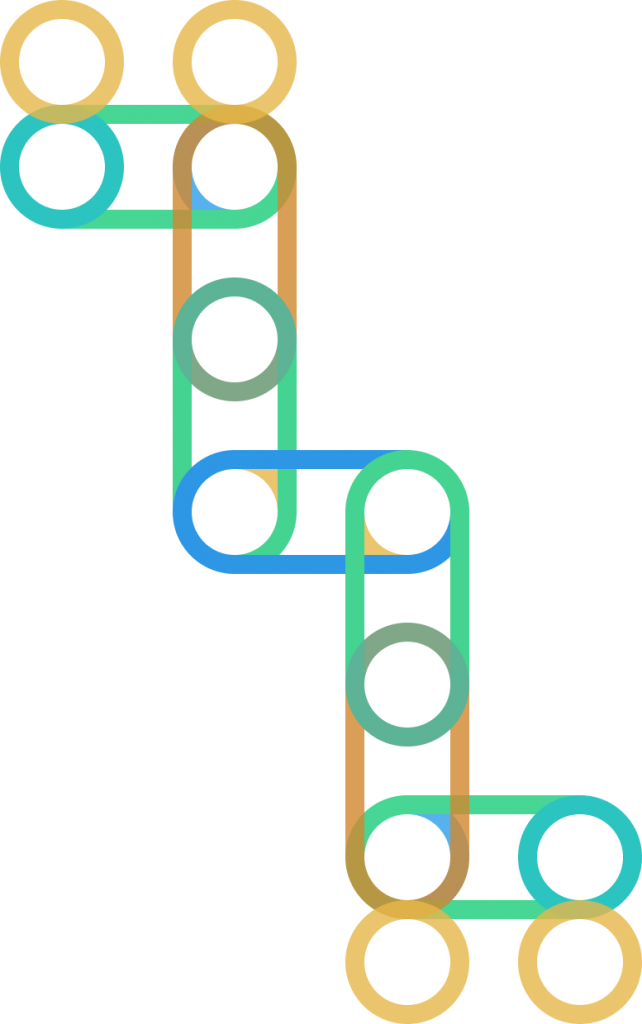
Heralded as a multi-billion dollar “game changer” for global consumer goods companies that have promised to incorporate 100% recycled content to their products, chemical recycling and depolymerization has taken on an almost holy significance in the polymer industry’s quest for full circularity.
Even though it is still widely accepted that the tried and tested process of mechanical recycling remains the most environmentally-friendly alternative for transforming post-consumer PET packaging into rPET, billions are being invested in chemical recycling projects to overcome some of the limitations of plastic recycling.
By promising to return waste into the monomers from which PET is originally made using processes such as hydrolysis, methanolysis, glycolysis, ammonolysis, and aminolysis, advanced recycling has an alchemistic allure that’s hard to resist.
Dr Markus Steilemann, President of PlasticsEurope and CEO of Covestro says the two forms of recycling together are essential for polymer producers and packaging companies to transition to a more sustainable, less disposable future.
“Based on a unique approach to the circular economy, we believe that embracing and investing in a hierarchy of technologies, ranging from mechanical to chemical recycling, delivers the optimum circular solution for the value chain with less impact on the environment. This approach will enable the plastics industry to achieve its ambitious recycling targets and will contribute to more sustainable living,” he says.
A Big Opportunity for Big Investments
Research by McKinsey & Company has outlined how the different chemical recycling alternatives could be responsible for as much as 50% of plastic stocks by 2030 if the industry follows through on its ambitious investment plans and meets with the right regulatory and economic environment.
The rollout of chemical recycling plants across the world coupled with the expansion of existing mechanical recycling facilities could create a scenario in which up to half of all plastic is recycled by the end of this decade.
“We outline a scenario for the plastics industry through which 50% of plastics worldwide could be reused or recycled by 2030—a fourfold increase over what is achieved today—and that also has the potential to create substantial value,” argues Thomas Hundertmark, McKinsey & Company’s global leader sustainability for energy and materials sector.
Bringing the rest of the polymer classes into line with recycling rates already being achieved by PET will be a welcome breakthrough, especially if the new technology encourages the extension of deposit and return systems to other waste flows rather than increasing competition for easily recyclable materials like PET.
The success of deposit and return systems for PET bottles shows what could be considered possible for other packaging types.
“Nine of ten countries with established DRS, in Europe, have achieved sorted for recycling rates of 83% or higher,” according to Petcore Europe. “These systems result in varied performance – it is currently estimated that the worst performers result in sorted for recycling rates of 22% while the best reach rates of 75%. This is with the exception of Belgium, who reports a sorted for recycling rate of 92% despite not having a DRS scheme in place.”
Forcing the issue, the European Commission has decided that 10m tonnes of recyclate should be utilized in the EU, by 2025. Moreover, all packaging in Europe should be either reusable or recyclable by 2030. To achieve this, the introduction of a European Union tax on plastic that doesn’t incorporate 30% of recycled content, introduced in 2021, coupled with support for circular initiatives has proven to be the catalyst for significant investments in chemical recycling plants in Europe.
The region is pointing the way to the rest of the world.
Furthermore, with the price of oil pushing through $100 per barrel, alternatives to virgin fossil fuel stocks have become increasingly attractive.
McKinsey estimates that with an oil price above $75 per barrel, plastics reuse and recycling could generate profit-pool growth of as much as $60 billion for the petrochemicals and plastics sector, a figure that would represent nearly two-thirds of the polymer industry’s possible profit-pool growth by the end of this decade.
To achieve the 50% figure, waste-recovery capital investment of about $15 billion to $20 billion per year would be required, according to McKinsey, representing around 20% of $80bn to $100bn invested by the global petrochemical and plastics industry each year over the past decade.
Innovative Investors Lining Up
Leading the charge in new PET chemical recycling investments is the French chemical recycling specialist, Carbios, which recently inked a deal to build the world’s first industrial-scale enzymatic PET bio-recycling plant, with a processing capacity estimated at 50,000 tons of post-consumer PET waste per year, equivalent to 2 billion PET bottles or 2.5 billion PET trays.
Underpinned by a joint-investment with Indorama, the world’s largest producer of PET, the project uses enzymes to accelerate its chemical recycling process. Used PET flakes are mixed with the patented cutinase enzymes —produced by Denmark- based biotechnology company Novozymes — and warmed to a little above 60 degrees centigrade.
The capital investment required for the new plant in Longlaville, France is expected to be around €150 million for Carbios core technology, including in particular an additional purification step, which has been integrated into the process for the Indorama venture. An estimated additional €50 million investment will be allocated for the infrastructure preparation of the site.
Carbios innovation, it claims, allows infinite recycling of all types of PET waste as well as the production of 100% recycled and 100% recyclable PET products, without loss of quality.
“Plastic and textile waste is now a precious raw material enabling the circular economy to become an industrial reality,” says Carbios Chief Scientific Officer, Alain Marty. Testing of the proof of concept has already taken place at a smaller facility in France where within 10 hours, 95% of the plastic fed to Carbios’ reactor, the equivalent of 100,000 plastic bottles, can be converted into monomers, which are then filtered, purified, and prepared for use in plastic manufacturing. The product that emerges is indistinguishable from the petrochemical-based substances used to manufacture virgin PET.
Other circular economy startups and intrapreneur initiatives by some of the world’s largest polymer producers are not far behind Carbios in their plans to build industrial-scale plants using enzymatic or other chemical processes that offer a back-to-back recycling future.
GR3N, Garbo, Ioniqa and Loop Industries are all in various stages of funding and development for similar projects in Europe and the US.
Cost and Life Cycle Assessment Comparison
Given the technology’s long-term attractions, its ultimate success will rely on startups like Carbios being able to bring the costs down as currently recyclates taken from post-consumer waste can be as much as twice as expensive as virgin fossil fuel stocks depending on the price of oil.
Analysis by the National Renewable Energy Laboratory, which has been assessing the potential of enzymatic recycling in the US estimates that PET monomers produced through this method could cost at least $1.93 per kilogram compared to a historic price range of between $0.90 and $1.50 per kilogram since 2010 for virgin, petroleum-based monomers over the last decade.
“At the beginning, sure, it will be a little more costly,” says Marty, “but we will reduce, with experience, the cost of this recycled PET.”
The differential isn’t stopping polymer producers, packaging companies, social impact investment funds and consumer goods companies from betting big on the technology as the solution to the world’s plastic waste problem. In Europe alone, there are plans to invest up to $7.9bn in chemical recycling facilities in 2030.
Chemical recycling in Europe could be producing 1.2Mt of polymers in 2025 and 3.4 Mt in 2030.
McKinsey’s forecast points to a sharp increase in global mechanical recycling rates from the current level of 12% of total plastics volumes to between 15% and 20% of a much larger projected total of plastics output by 2030. Total polymer production is expected to reach 1bn tonnes by 2050, compared to 367m tonnes in 2020.
Driving the upward trend in overall recycling rates of plastics are the elevated rates of PET bottles and trays being recycled. Petcore estimates that 49% of total PET rigid packaging arisings were collected and sorted for recycling across the European Union in 2020 and this is only expected to grow even further with the expansion of recycling facilities of both types.
Monomer recycling, although it is inherently restricted in its application to condensation-type polymers such as PET, McKinsey says, has the potential to generate some of the highest plastics recycling profitability levels in the next 10 years.
Possible Game Changer for the Oil Industry
A reuse level of as much as 50% would also profoundly affect new plastics production. By 2030, up to almost one-third of plastics demand could be covered by production based on previously used plastics rather than from “virgin” oil and gas feedstocks, according to McKinsey.
This estimate is based on a high-adoption scenario, comprising a massive increase in mechanical recycling volumes, a takeoff in pyrolysis, and oil prices at around $75 per barrel. Taking this scenario further, McKinsey estimates that as much as 60% of plastics demand could be covered by production based on previously used plastics by 2050.
“This will substantially reduce the amount of oil required to cover global plastics demand, with projections suggesting oil demand running 30% lower than a business-as-usual scenario. This outcome would require revisions of recently published forecasts that show petrochemicals making the largest contribution to oil demand growth over the next two decades,” says Hundertmark.
Under the high-adoption scenario, the cost position of plastics-waste-based feedstocks—via mechanical recycling, monomer recycling, or reuse through pyrolysis or other feedstock supply—could potentially be so attractive that they could account for two-thirds of the profit-pool growth of the petrochemicals and plastics industry by 2030, according to McKinsey.
Revenues generated from polymers are set to grow from $533.6bn in 2019 to $838.5 billion by 2030, at a 5.1% CAGR, according to P&S Intelligence.
Adapting to this rapidly changing landscape is crucial for companies further downstream. In its research, McKinsey sets out the importance of establishing partnerships to accommodate this seismic shift, or the need for stakeholders to identify acquisition targets that “could help players gain access to needed technology or secure sufficient access to waste-plastics feedstock supply”.
As the investment panorama heats up many of the biggest polymer producers are investing in start-ups, undertaking promising process development and collaborating with research institutes.
In the case of feedstock, the same startups are forging long-term supply agreements with municipalities, waste-management companies, landfill sites, and, in effect, any player with access to large quantities of plastics waste. Possible strategies could even include back integration, whereby a petrochemical company acquires or establishes a waste-collection operation, says McKinsey.
Likewise, plastics companies may want to boost their investments in mechanical recycling operations to facilitate rapid expansion of their offering to include recycled resins and plastics-recycling companies in Europe have been acquired by major petrochemical companies in a trend likely to continue, according to McKinsey.
Petrochemical and plastics companies have to be prepared to adopt a different business model, where they will have to source plastics-waste supply from a large number of scattered players rather than getting their raw materials in bulk from one source.
“Chemical recycling is a game changer and a key building block of the circular economy – not only in Europe,” says Lucrece Foufopoulos, executive vice president of Polyolefins and Circular Economy at Borealis. “This increased investment confirms the determination of the industry to address the problem of plastic waste and supports the EU Green Deal’s climate and sustainability ambitions. However, this is just a starting point, and sizable investments are still needed to fully capture the value of this technology.
Companies making waves in this space:
Garbo
https://garbo.it/en/chempet/
Ioniqa
https://ioniqa.com/
GR3N
https://gr3n-recycling.com/
LOOP Industries
https://www.loopindustries.com/en
Carbios
https://www.carbios.com/en/
Lyondell Basell
https://www.lyondellbasell.com/
Infinity Recycling
www.infinity-recycling.com
Honeywell
UpCycle Technology (Mixed Plastic)
https://uop.honeywell.com/en/products-and-services/upcycle-plastics-recycling
References:
- McKinsey Research / How Plastics Waste Recycling Could Transform the Chemical Industry
- Carbios to build in France its first-of-a-kind manufacturing plant for fully bio-recycled PET in partnership with Indorama Ventures
- LyondellBasell Invests in Infinity Recycling Venture Fund to Advance the Circular Economy
- TotalEnergies and Honeywell sign a strategic agreement to promote the development of advanced plastic recycling
- America’s Largest Plastics Recycler Will Use Honeywell’s Advanced Plastics Recycling Technology
- Analysis of Thermomechanical Properties of Selected Class of Recycled Thermoplastic Materials Based on Their Applications.
Share it
THE HISTORY OF PLASTIC
Throughout the history of plastic, PET has been crucial in keeping food fresh with lightweight and durable packaging solutions that have helped reduce food waste for almost a century. Learn all about the invention of plastic and the important role it has played feeding people and saving the lives of humans and elephants in the adaPETation® timeline of the history of plastic.